Revolution
Realized
Innovative bending technology demanded by the future, the fully automated bending system.
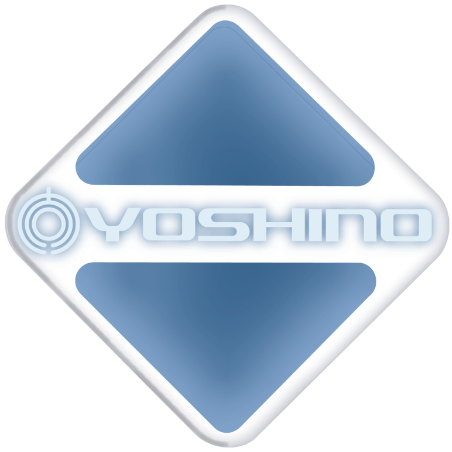
A world-class fully automated bending system created
by Yoshino Machinery's tradition and technology.
Yoshino Machinery’s tradition is not merely preserved—it evolves with time, continuously driving the creation of new value.
By fusing a legacy of skilled craftsmanship with the power of cutting-edge technology, we have developed a world-class fully automated bending system.
This system simplifies complex processes, enhances safety, and significantly boosts productivity, redefining the future of manufacturing.
The depth of tradition and the force of innovation converge to create unparalleled value—all embodied in this singular machine.
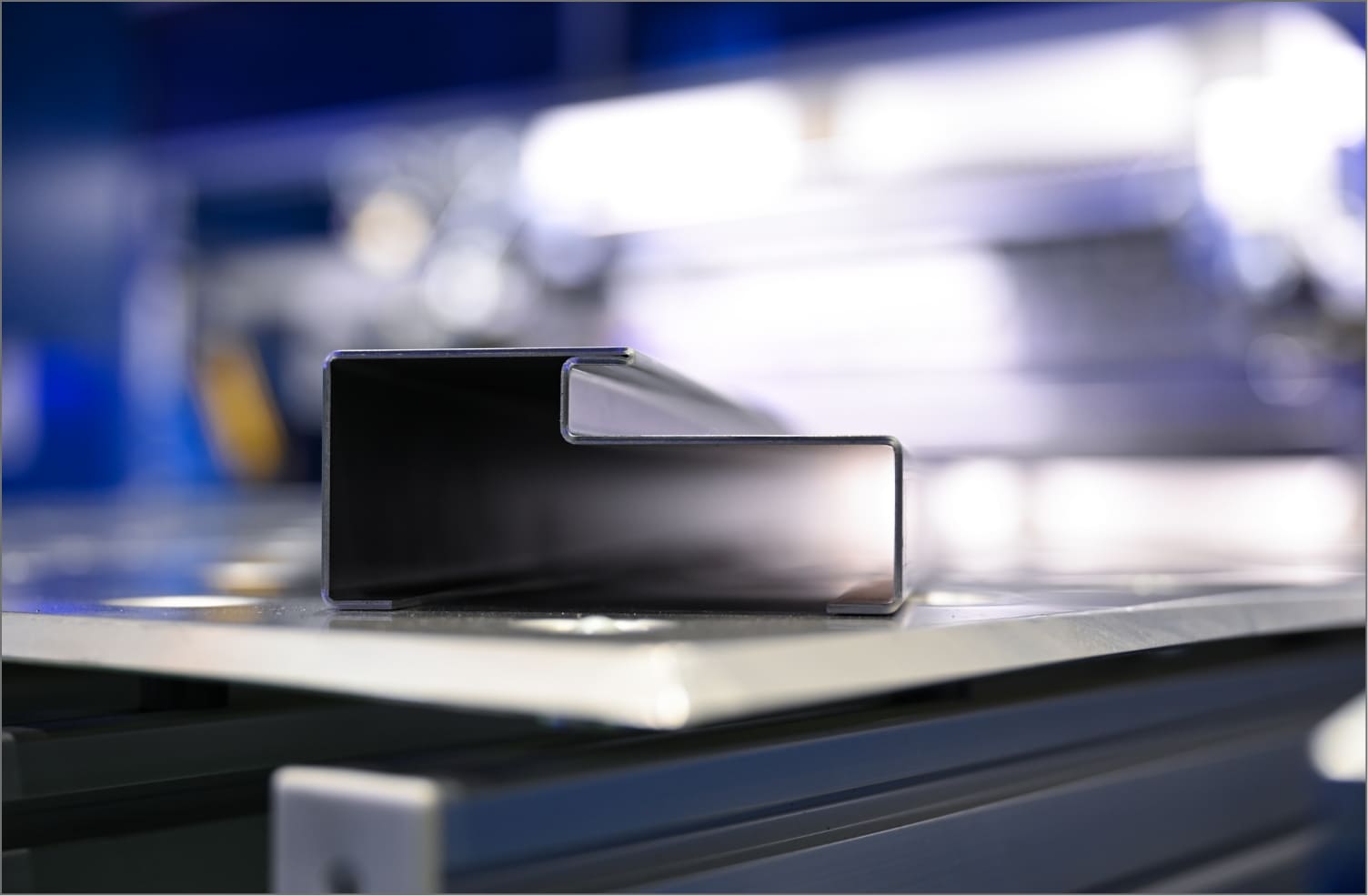
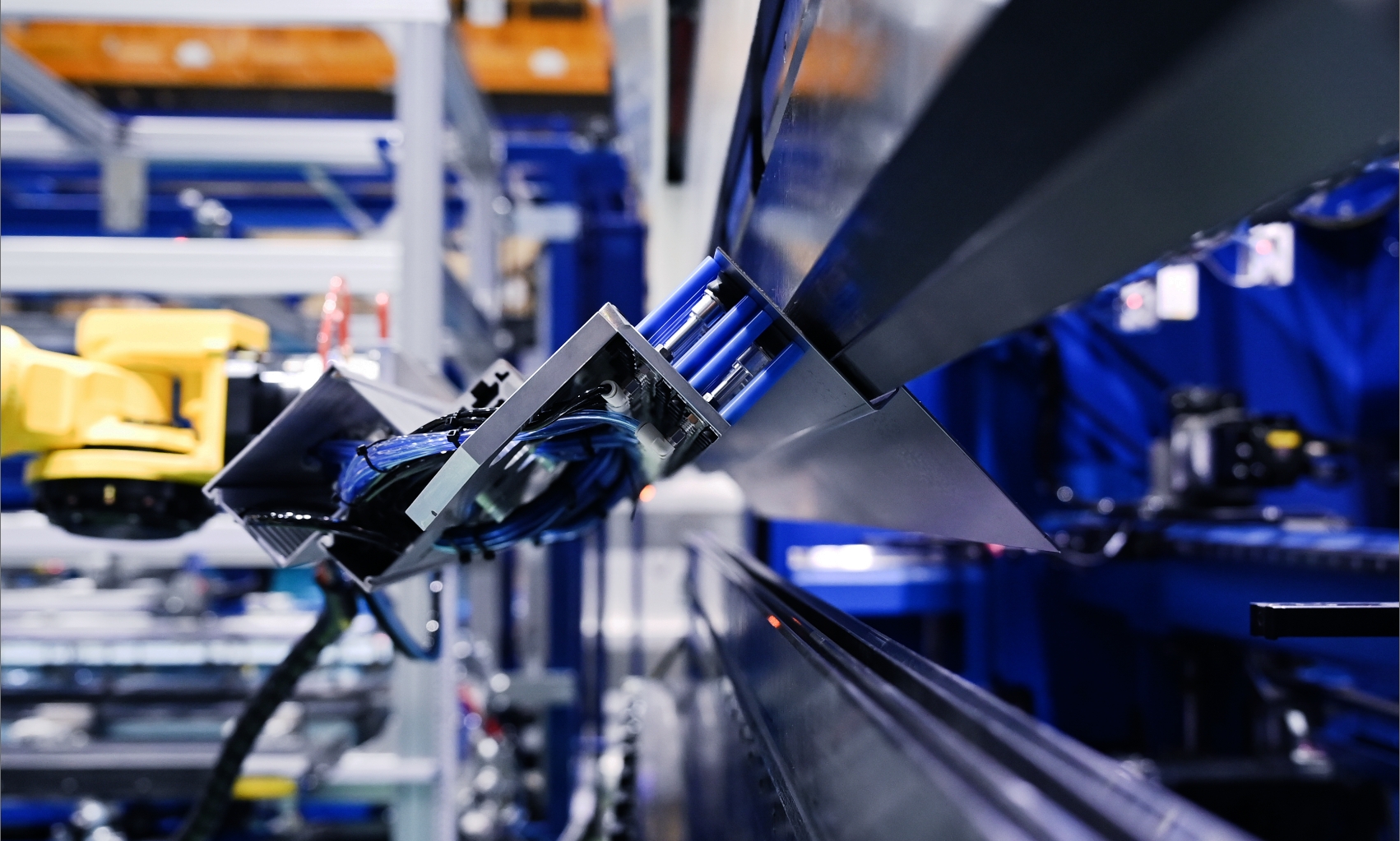
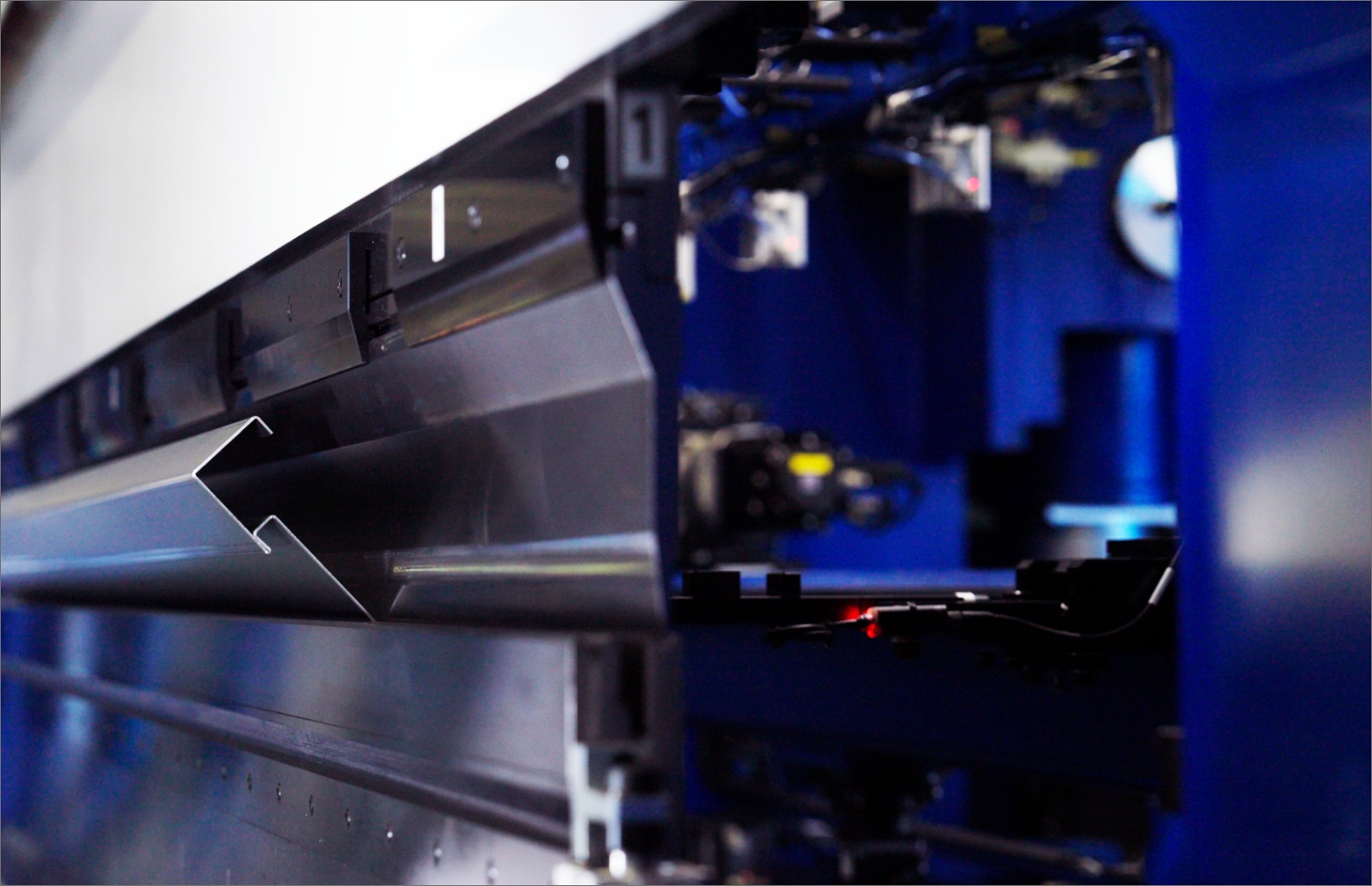
Features of the Fully Automated Bending System "YSP-R Series"
feature
01
High Precision
Micron-Level Accuracy in Sheet Metal Processing
The YSP-R Series fully automates the bending process by optimizing operations based on drawing data. This ensures a level of precision that is difficult to achieve manually. Even for long sheet metal pieces and complex bending shapes, the system maintains high reproducibility and consistently delivers superior product quality.
02
Efficiency
Automation That Significantly Boosts Productivity
By eliminating the need for manual teaching, the system drastically reduces setup time.
It also flexibly adapts to high-mix, low-volume production, eliminating bottlenecks in conventional bending operations. This enables manufacturers to process more products in less time while reducing dependence on human labor.
03
Sustainability
A Future-Ready System That Balances Environmental Impact and Safety
Designed with energy efficiency in mind, the YSP Series reduces operational costs while minimizing environmental impact. By eliminating the need for direct human intervention in hazardous tasks, the system significantly enhances workplace safety. It is not only a solution for sustainable manufacturing but also a benchmark for the future of the manufacturing industry.
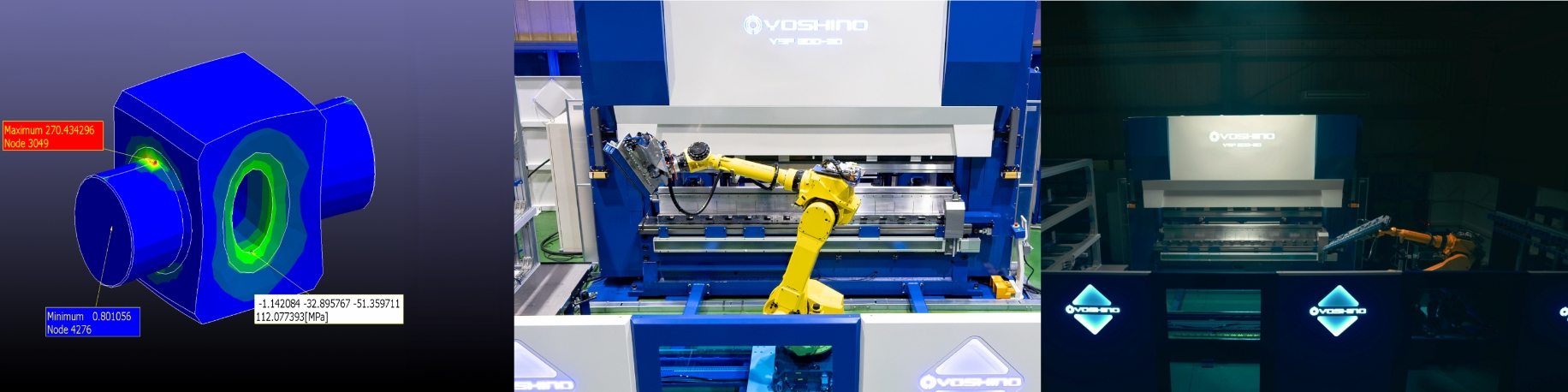
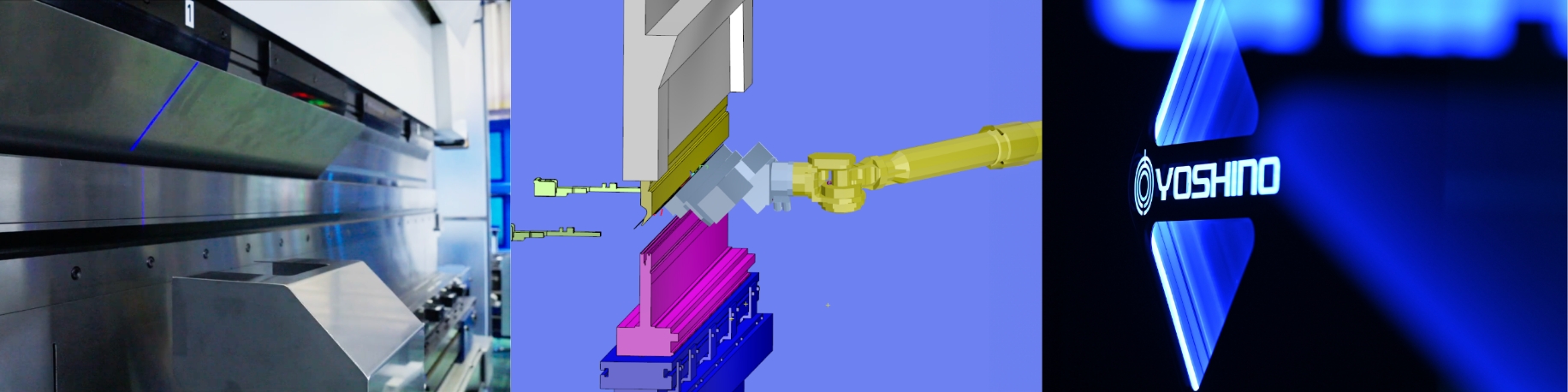
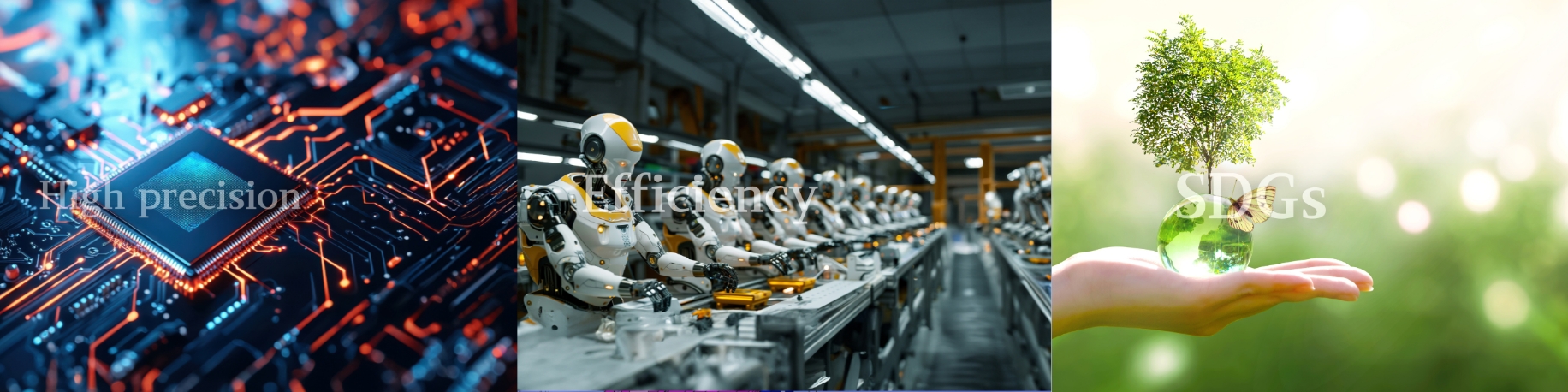
Mechanism of the Fully Automated Bending System "YSP-R Series"
performance
The YSP-R Series seamlessly integrates cutting-edge software and hardware, executing operations through the following steps:
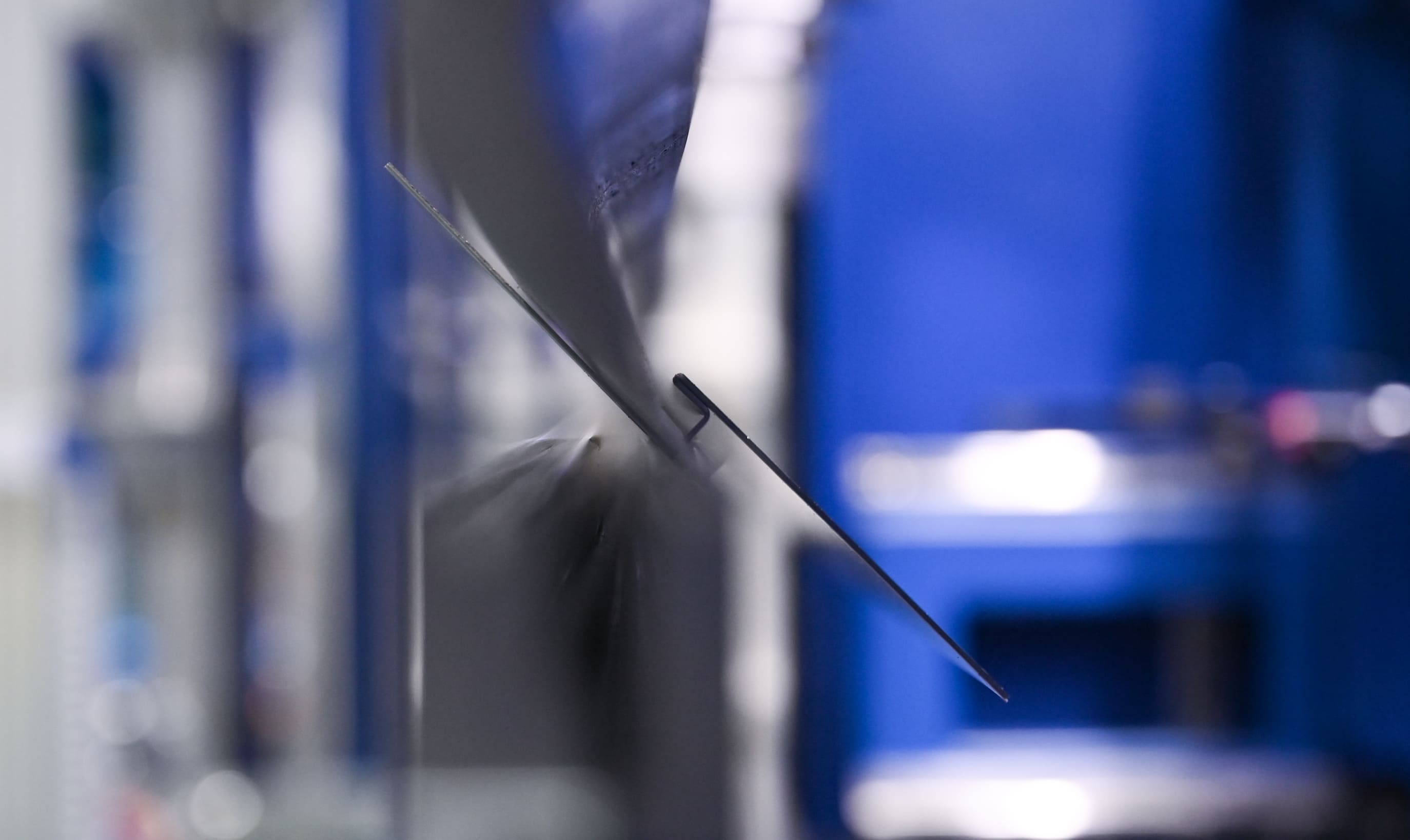
01
Drawing Data Input
Simply upload 3DCAD(STEP) or DXF or DWG files, and the system instantly analyzes shape data, material thickness, bending angles, and radii.
It then calculates the optimal processing sequence in real-time, significantly enhancing setup efficiency.

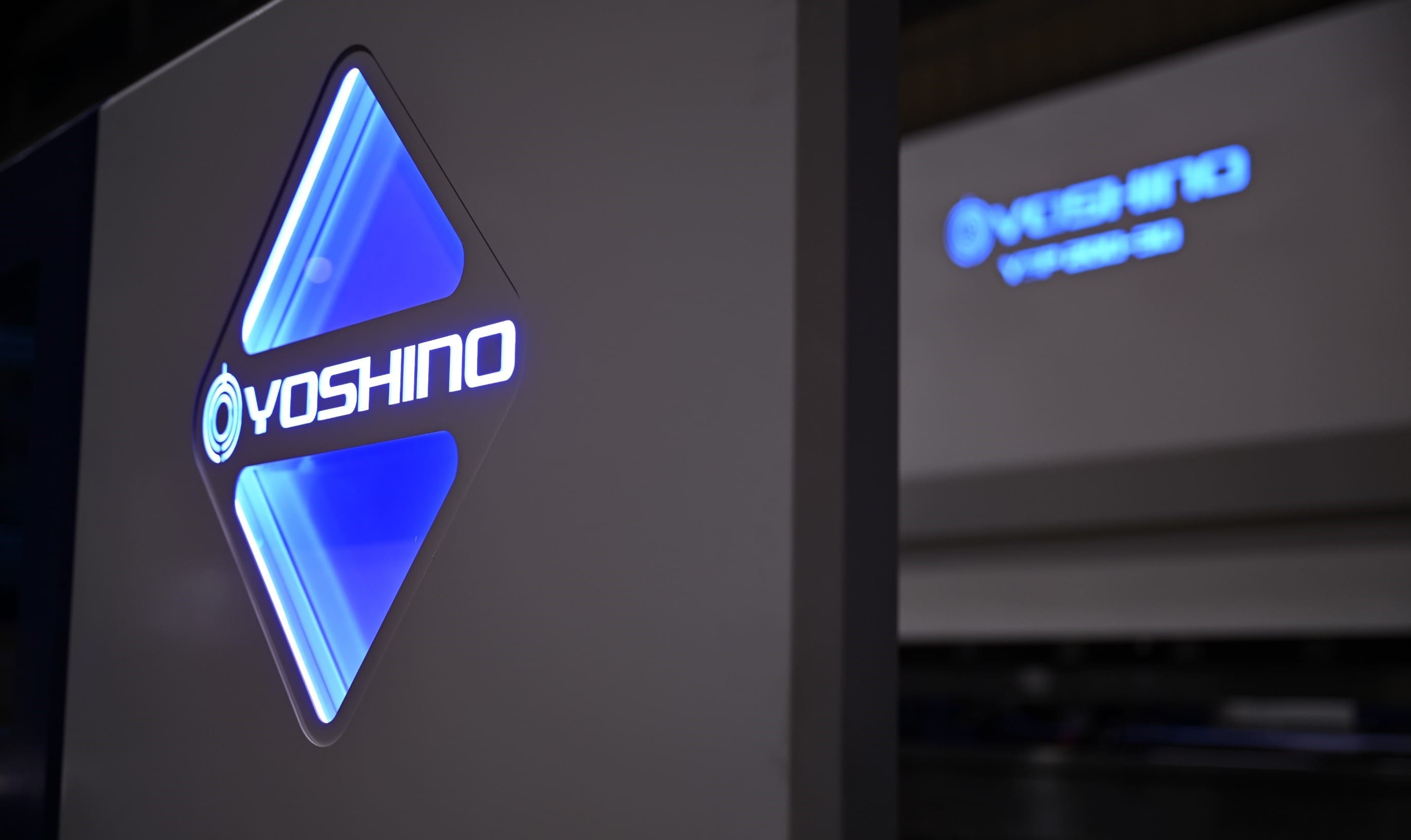
02
Automatic generation and algorithm-based optimization of bending sequences.
Automatically generating bending sequences using a proprietary algorithm.
Advanced algorithms developed by Yoshino Machinery automatically generate the most efficient bending sequence while avoiding potential interferences and constraints.
The system intelligently selects the most suitable dies from multiple options, accurately simulates material deformation, and prevents processing errors.
Automatic Validation Feature
The software performs a simulation to verify whether the design can be executed as intended. If necessary, it provides optimized correction suggestions.

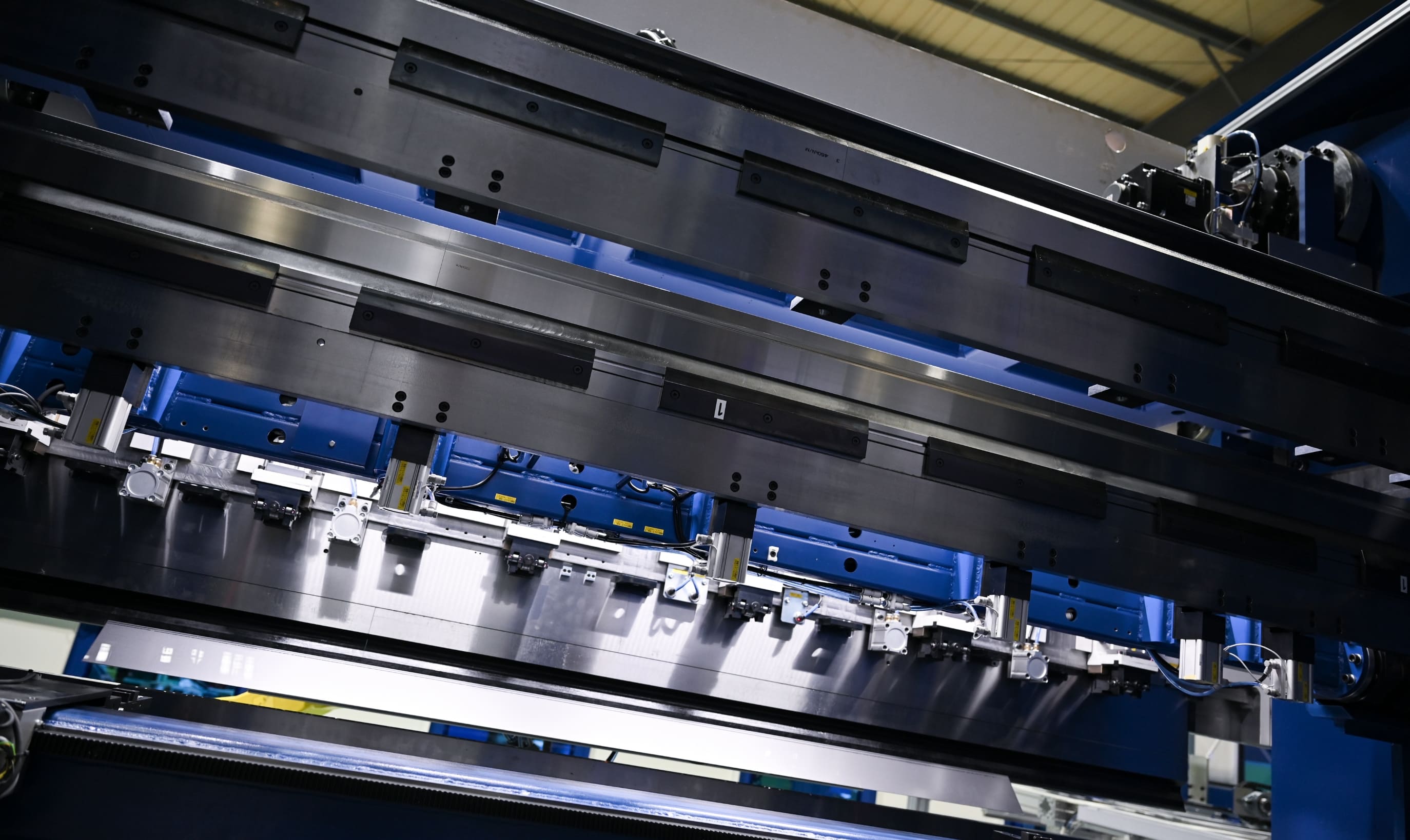
03
Automatic Tool Changer (ATC)
(Auto Tool Changer)
Instant Molds Replacement
Yoshino’s ATC enables seamless, high-speed switching of long molds without downtime, allowing smooth and efficient processing of complex shapes.
Workload Reduction
Eliminates the need for manual setup, significantly reducing operator workload. The reduction in setup time greatly enhances productivity.

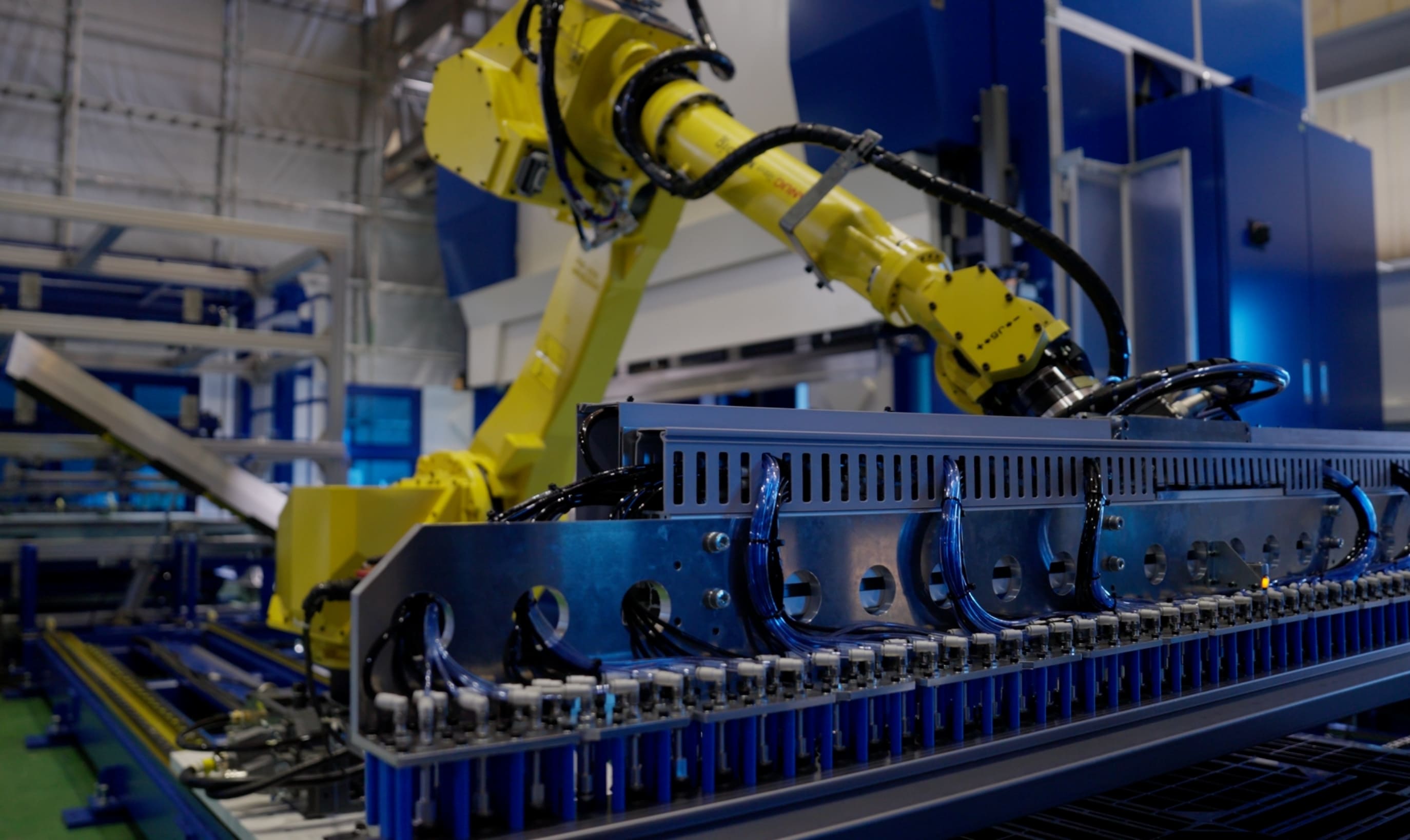
04
Robot Control and Automatic Bending with Advanced CAM
No Need for Teaching Operations or Press Brake Operation
The proprietary CAM system enhances coordination between industrial robots and press machines.
The advanced CAM automatically generates robot trajectories and press brake movements, eliminating the need for teaching operations and manual press brake operation.
This significantly reduces operator workload.
Additionally, the advanced algorithm allows for flexible adaptation to high-mix, low-volume production.
Compatible with integration into higher-level systems.
Safety Measures
Equipped with sensor-based safety fences. If an intrusion is detected, the robot automatically stops to ensure operator safety.

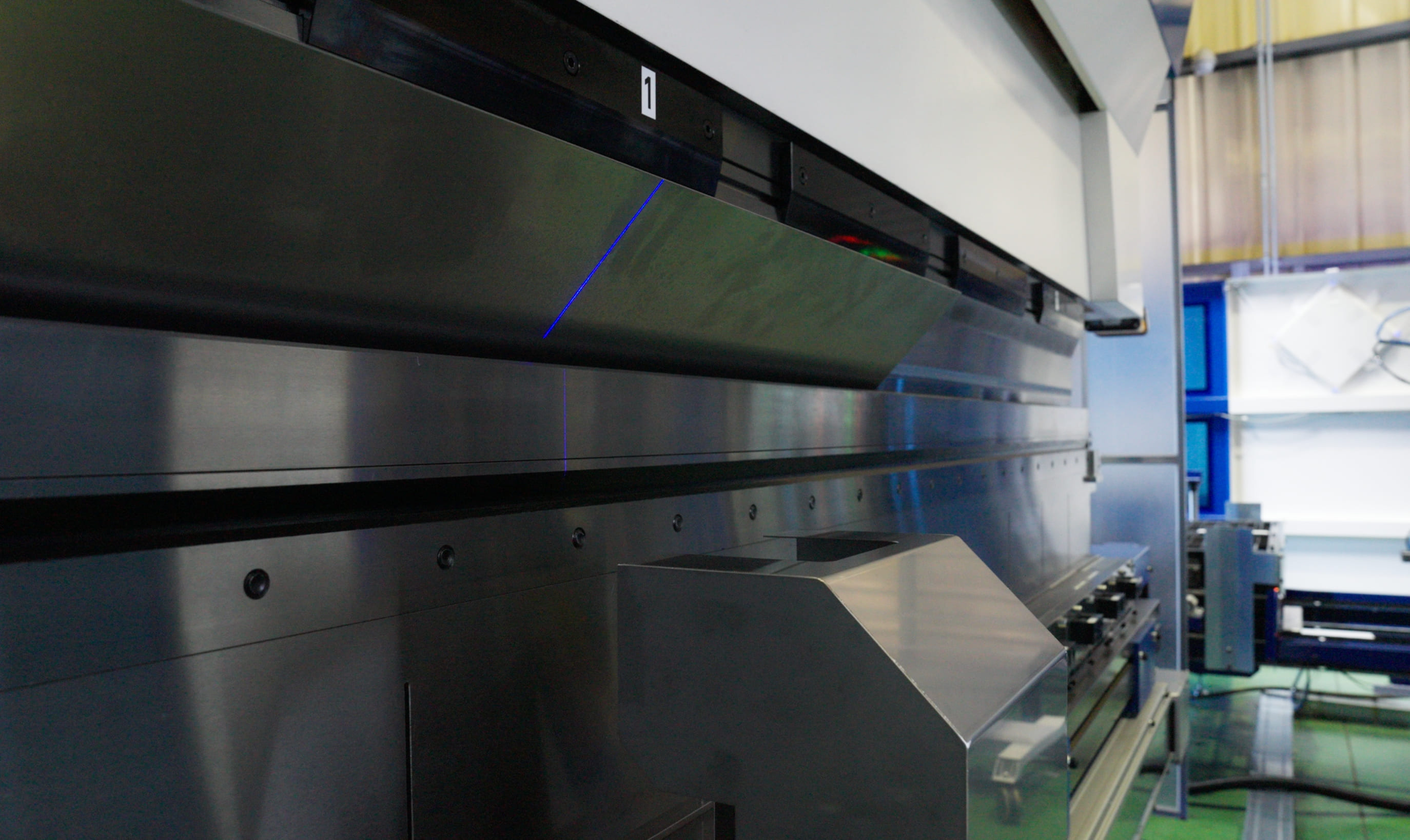
05
High Quality & Precision
Angle Sensor
The laser angle sensor enables precise angle control by compensating for spring-back.
Automatic Crowning
The automatic crowning system minimizes press brake-specific deformations, ensuring exceptional straightness accuracy.

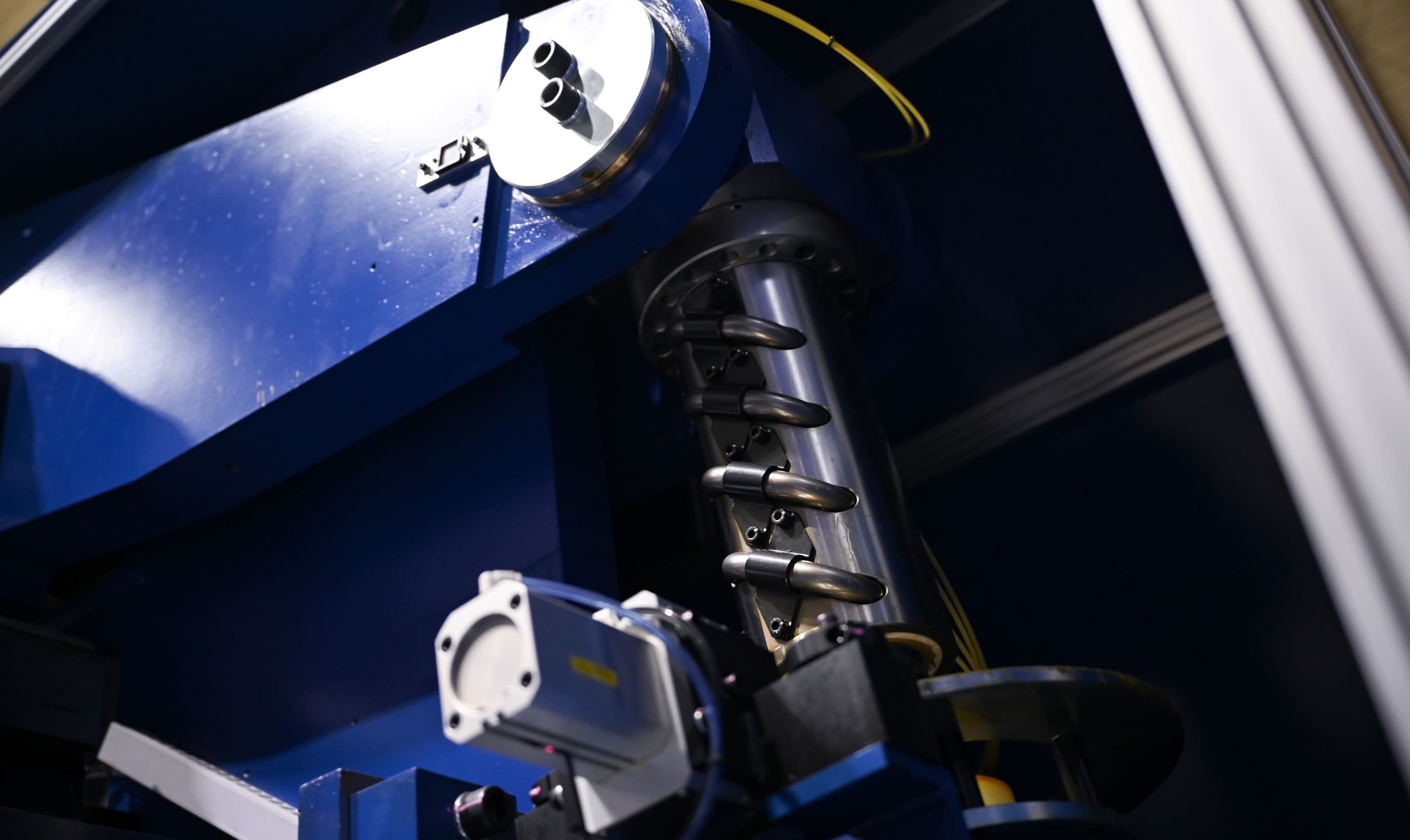
06
Environmental Performance & Sustainability
Energy-Efficient Design
Eliminates hydraulic drive by adopting servo motors and precision ball screws.
Reduces power consumption to one-fourth compared to conventional hydraulic press brakes.
Contribution to Carbon Neutrality
Significantly reduces CO2 emissions, supporting a sustainable manufacturing environment.
Designed to meet stringent environmental regulations in global markets.

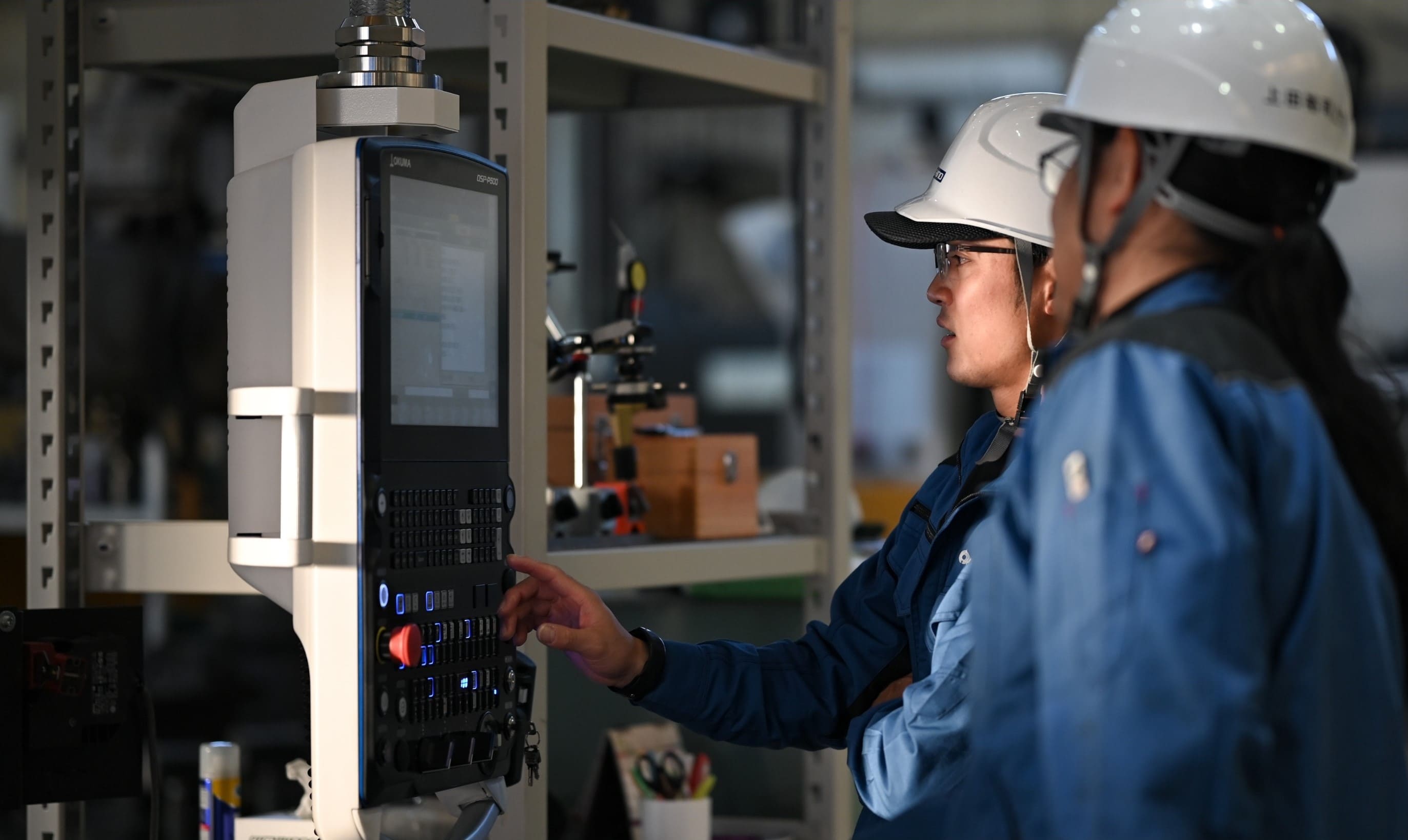
07
Interface & Usability
User-Friendly Design
Features an intuitive touchscreen interface with multilingual support.
Suitable for both beginners and experts, ensuring easy use in international markets.

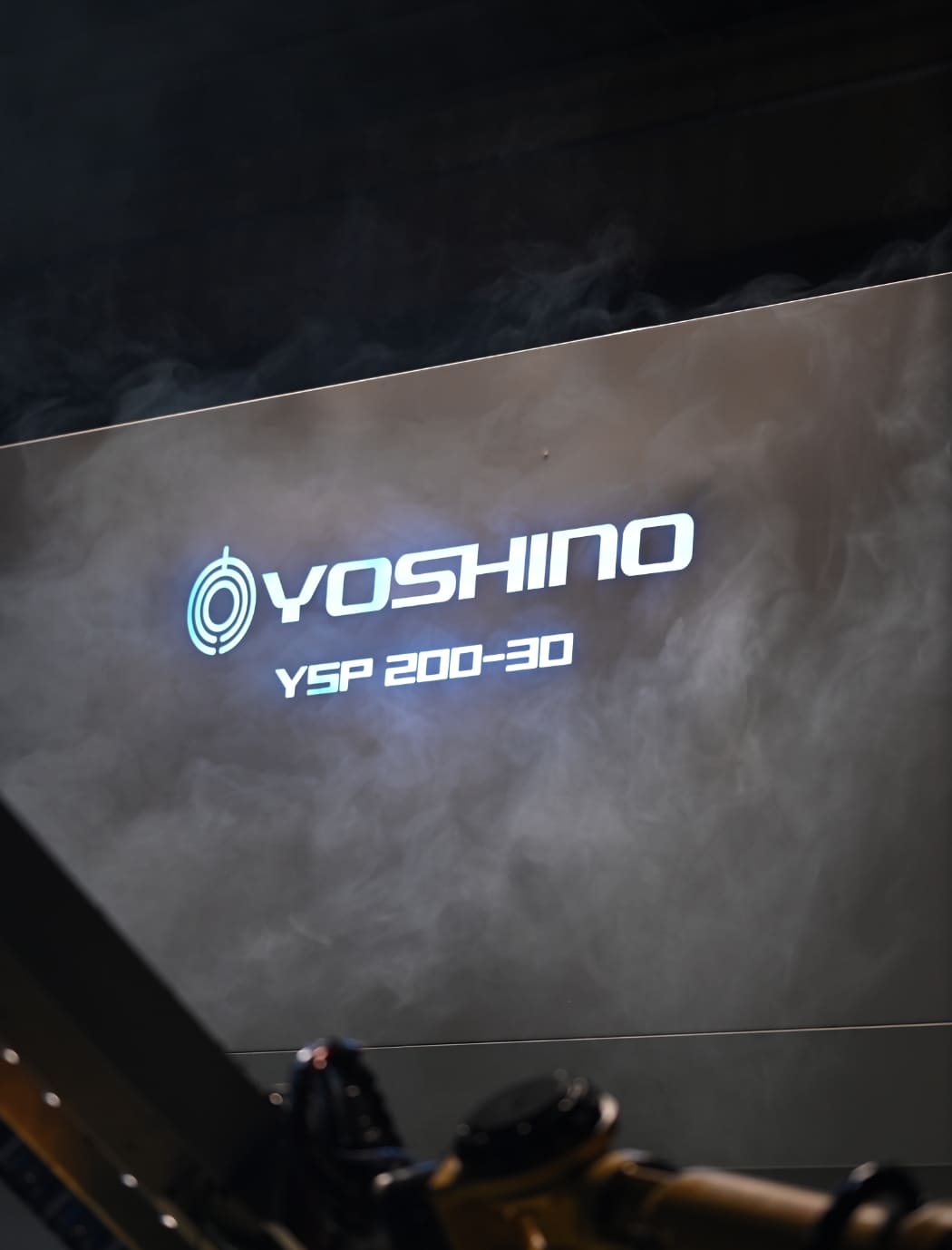
Specifications of the Fully Automated Bending System "YSP-R Series"
machine
specification
-
01Robot System Specifications→
-
02Basic Press Brake Specifications→
-
03Software Specifications→
-
04Environmental Performance→
-
05Installation Requirements→
- Production Management System
- Compatible with integration into existing systems or deployment of new systems.
- Software
-
The industry's first integrated CAM for sheet metal robot systems
※Includes a sheet metal CAM system that supports automatic tool changing (ATC) for long molds and automatically generates robot trajectories.
- Robot
- 6-axis industrial robot (compatible with specified manufacturers) + travel axis
-
Workpiece Loading/
Unloading - Leverages extensive experience in automated line design to meet diverse needs.
- Safety Zone
- Provides safety devices and protective fences tailored to the installation environment.
- Options
-
・Automatic Angle Correction (Equipped with Angle Sensor)
・Automatic Crowning System
・AI-Powered Interactive IoT Monitoring System
・Mode Switching Capability
※ Supports manual operation during the day and automatic robotic production at night.
- Maximum Processing Length
- 4m
- Maximum Pressing Force
- 400 tons
- Ram Movement Speed
-
Electrically Driven, Among the Fastest in the World
(Low Speed: 10mm/s, High Speed: 275mm/s)
※ These speeds are based on the YSP200-30 model.
-
Automatic Tool Setup Function
※ Optional -
・Long Molds ATC (Upper: 4 types, Lower: 3 types + Hemming Mechanism)
・Side Stocker-Type ATC
- Repeat Positioning Accuracy for Each Axis
- ±0.01mm or less
- Remarks
-
Custom specifications are also available.
For detailed press brake specifications, please refer to the product page.
- Machine Operation
- Touchscreen Compatible
- CAM
-
・CAD/CAM Data Import
・Automatic Search for Dies and Bending Sequences
・Automatic Generation of Robot Trajectories
- Multilingual Support
-
Japanese, English, Korean, Chinese, German, etc.
(Supports a wide range of languages.)
- Energy Efficiency
- Reduces power consumption to one-fourth of conventional levels (highest efficiency).
- Noise and Vibration Reduction Measures
- Reduces noise and vibration, ensuring a comfortable working environment.
- Oil-Free
- Servo motor-driven to reduce maintenance workload.
- Power Supply
- Three-phase 200V/400V, 50/60Hz
- Pneumatic Pressure
- 0.5MPa
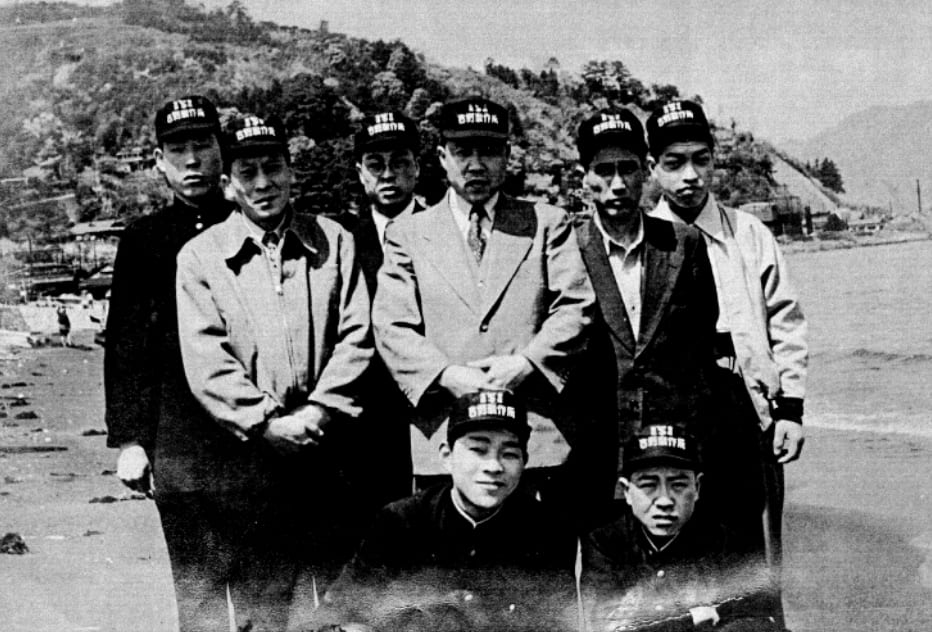
With a 70-year history, it has evolved from a subcontractor into a global manufacturer, mastering precision processing technology.
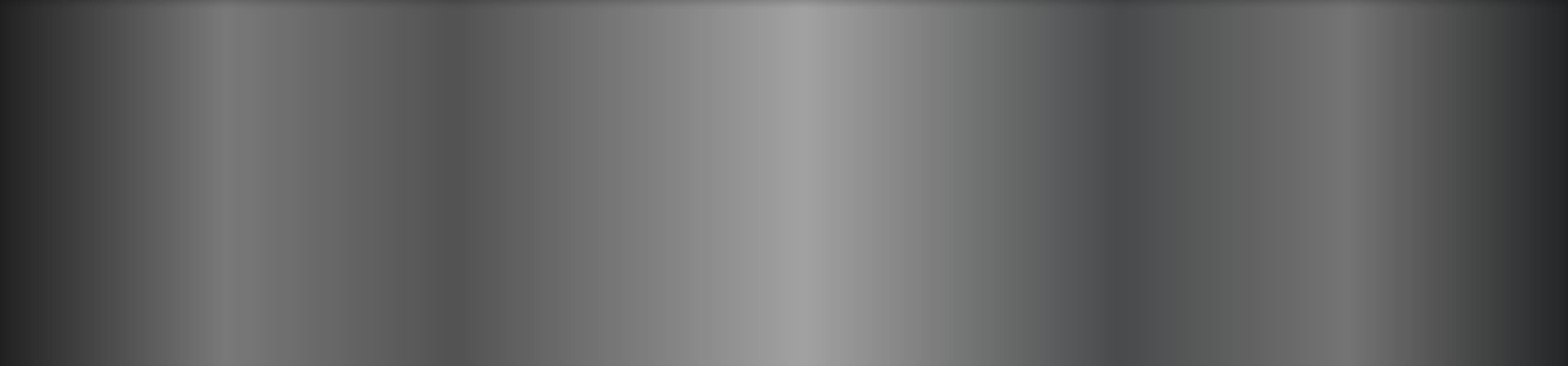
TEL+81-90-1893-9038
or +81-43-312-5900
Reception Hours: 9:00 AM - 6:00 PM (Closed on weekends and public holidays)